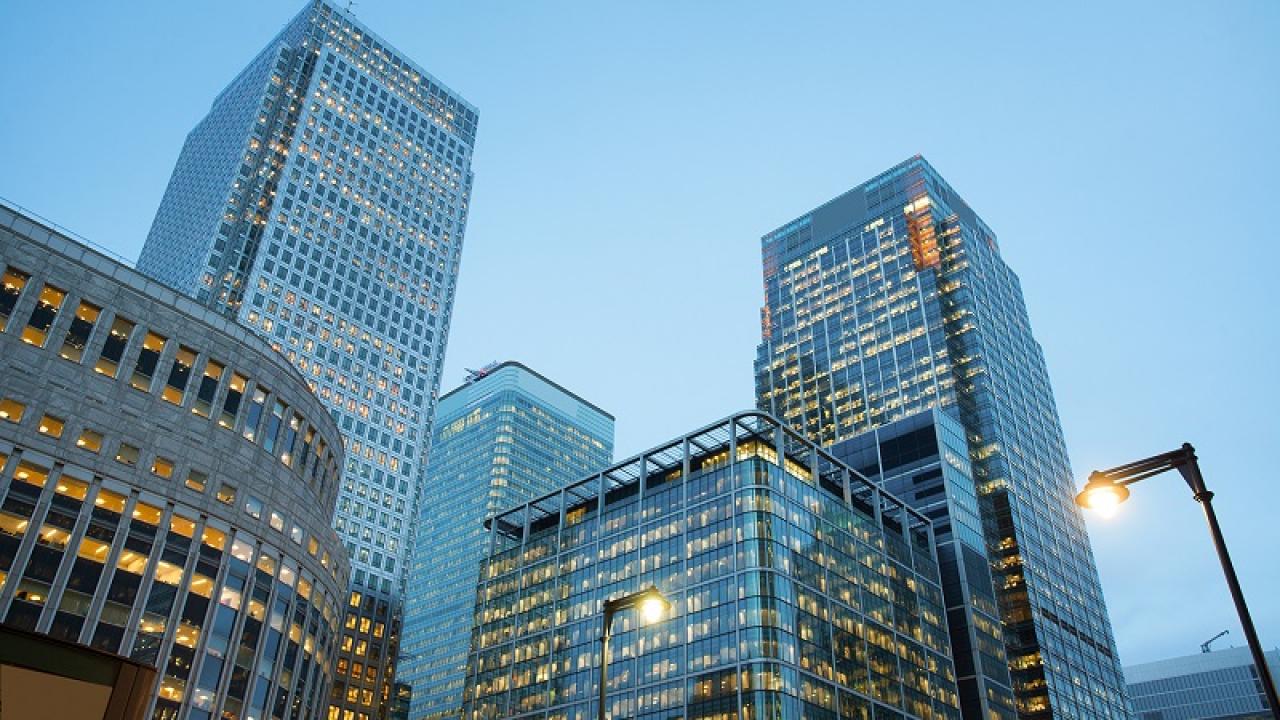
Formed in 1947, Lignacite has continued to develop new mixes and designs for their building blocks. Chairman Giles de Lotbiniere explains why the traditions of innovation, development and ingenuity remain such strong characteristics of this successful family business.
In 1947, Sir Edmond de Lotbiniere was approached by an inventor with a new mix design for blocks containing wood. It was a revolutionary building material and 75 years on, the business he created remains committed to continuing an extensive R&D programme ensuring it stays at the forefront of the construction industry.
Photo: Giles de Lotbiniere
Q: Has the constant and close family link been one of the key instrumental factors in the continued growth and success of the company over the last 75 years?
A: We are into our fourth generation now, and I do believe it remains important. Not only does it feel good that our family remains at the centre of the business, but it is also pleasing that we have a number of other fathers and sons who work here. There is something important about those family connections that have remained with the company over the years.
My own career started when I was 30. At that time, my grandfather was still very much in charge. I had spent eight years as a soldier prior to joining the business. When I arrived, I was given all the jobs that no one else wanted to do, but it meant that I had a great early insight into every part of our business. One of my first tasks involved quality assurance and producing a BSI manual for everything we do. I then moved on to roles in sales and production, and I was also involved in the complete refurbishment of our Essex factory. I really did dip into each and every aspect of the business until I eventually followed on from my father as MD.
Photo: Lignacite's production facility at Brandon
Both of my sons are now involved in the business, with one actively learning the ropes. My other son is taking a little break having worked for us for several years. He will be trying his hand at something very different, but he will hopefully return to the business in the future.
Q: The origins of the company are based around product innovation and the new mix designs for blocks dating back to 1947, has that quest for developing new products and new solutions been the main driving force?
A: When my grandfather was approached by an inventor with a new mix for concrete blocks, he immediately saw the potential and decided to give it a go. Those early products were all made by hand in Brandon. The special admixture was regarded as the magic ingredient that made the blocks so different and so much better, but it was also the most expensive ingredient. When the supply of the special admixture ran out, my grandfather decided to carry on making the blocks by hand and these blocks proved even better than the original ones. It turned out that the magic ingredient was actually the wood, not the special admixture.
The addition of wood in our blocks gives them a very good fire rating. Conventional concrete made with stone ultimately shatters under intense heat, whereas the wood in our blocks is locked in, denying a supply of oxygen to the flames. This means the blocks calcify and harden in a fire, giving superior performance. That innovation continues to be important to us as a business, and we are constantly searching for ways to make blocks that are lighter, warmer, and greener.
Photo: Lignacite trucks delivery blocks on-site
Another interesting point to note is the exothermic reaction of the cement in our design mix, which produces all the natural heat required for curing. This means that our blocks have a very low embodied energy.
In some respects, I do feel we have remained ahead of the curve, especially when it comes to environmental awareness. We have always used recycled materials in our blocks and in 2013, we produced the world’s first carbon-negative building block. One of our ranges already contained 90% waste materials and the carbon negative block was truly ahead of its time. I’m not sure the industry was ready for it back then, but these days there is much more awareness and interest in high-performing products like that.
If my grandfather were to return to the business today, much of what we do and how we do it would be unrecognisable to him, but that spirit of innovation and the investment in research and development is something that would still be familiar. I think he would be surprised at the scale of what we do now and the number of projects in which we are involved. He would also be impressed to know, and be delighted to see, that the Lignacite mix has changed very little.
Q: The wider industry has been witnessing a more rapid culture change recently, particularly as regards the sustainability agenda, how has the company adapted to this shift?
A: We have always been an environmentally focused business, and we are always looking for ways to make improvements using recycled materials in our products. The whole carbon footprint of the business and everything we do from production to transportation has become much more important.
We are not necessarily a large producer, and we have always gone for the higher end of the market. As such, producing a high-quality product and maintaining accuracy in everything we do has been an important part of the company ethos since 1947. The processes we have employed within the business throughout the years have always been set at a high standard, and the testing of our blocks has remained vigorous.
Photo: Canada Square
We have been operating as a green and sustainable business for many years, so we have not really regarded it as a culture change. We have always sought to source materials as close to our site as possible. We draw water from our own borehole, and we generate electricity from solar panels on site. That said, we still want to create cleaner and greener plants, and we are now embarking on a £10m investment in a new factory at Brandon. This significant improvement to our production facilities will further reduce our environmental impact and enhance our sustainability credentials.
Unfortunately, I think there is still a lot of confusion within the industry regarding the sustainability agenda. As a business, we have always been very clear on our responsibilities, and we know the environmental benefits of the blocks we produce.
Q: The Government has set industry-wide Net Zero targets for 2050, but the company looks to be setting much more ambitious targets for itself. What are the key aspects of this drive to become greener?
A: We do aim to beat the 2050 deadline. We are working to our own 2030 deadline, and it is a dual approach, which involves both what we put into our blocks and the sustainable methods by which they are made. We have been working towards this goal for a number of years. We already put a lot of recycled and renewable aggregates into our products and as we’ve discussed, you don’t need much energy to produce concrete blocks. We’ve also recently implemented an app-based electronic proof of delivery (EPOD) system for deliveries dispatched from our Brandon plant, which we are hoping to roll out to our Nazeing plant in due course. The new plant at Brandon will use considerably less energy than the existing one and be far more efficient, so all of these factors combined will help us to reach that Zero Carbon target.
Q: Do you still get a sense of pride when you see your products used on so many existing and new landmark buildings and projects?
A: I still get a sense of pride when I pass one of our lorries out on the road. Knowing our blocks have been used in landmark developments, including the Shard, Gherkin, and six projects at the Olympic Park, is a definite source of pride. I am also proud of how far the business has come since 1947 and how many different projects we have been involved in. When my grandfather first started, he was generally supplying blocks for the agricultural market and farm buildings. Today, our blocks are used in some of the most iconic buildings in the world. We continue to work and collaborate with influential partners across the construction industry, and our products are held in extremely high regard.
To find out more about Lignacite's sustasinable concrete blocks click here.
Photo: Orbit and the London Stadium