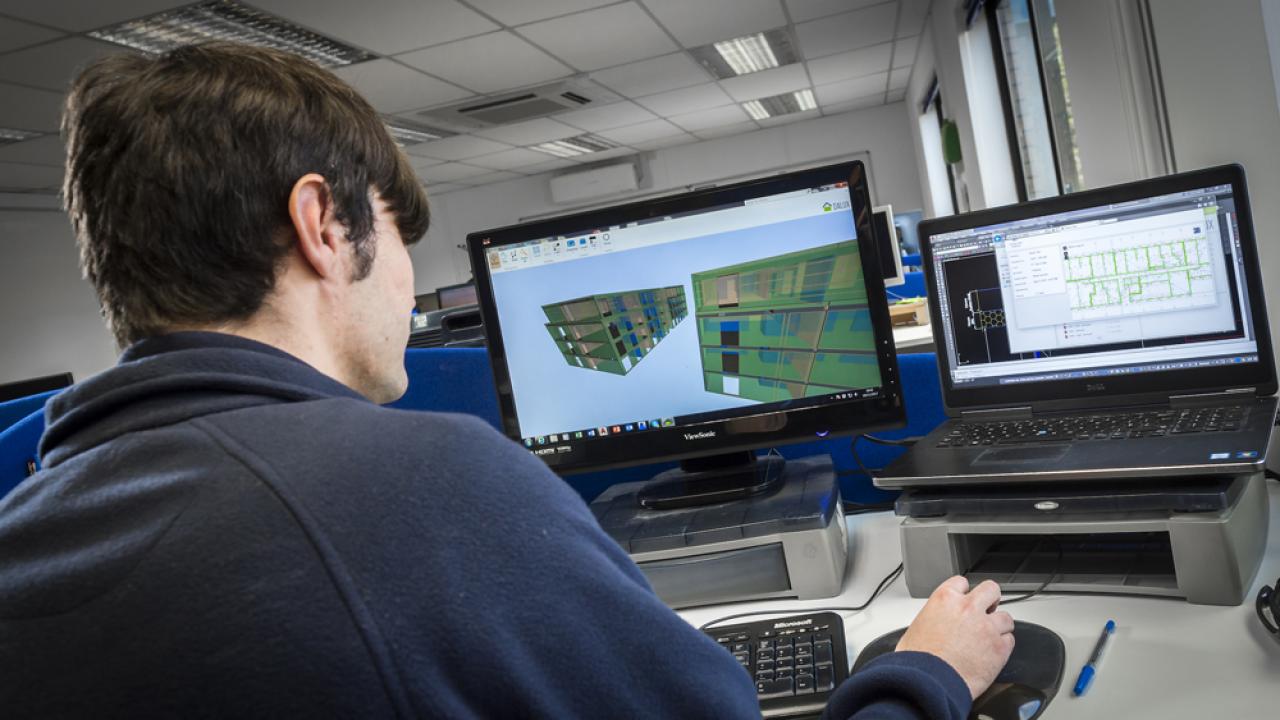
Mention modern methods of construction and often the next word in the sentence is ‘modular’.
The adoption of a single word to cover all forms of offsite construction is actually creating a misunderstanding throughout the industry.
Mike Fairey, of light gauge steel offsite manufacturer Fusion Building Systems, explains.
I probably need to start by back-tracking a little and explain what offsite manufacturing (OSM) is.
There's nothing new about OSM – it’s been used as a construction method for decades, the only reason more people seem to be talking about it now, is because it offers so many benefits over traditional building methods, for example:
• Safer working conditions
• Improved quality and standard of build
• Shorter and predictable build times
• Fewer materials and deliveries to site.
The OSM process starts with design. Architects and offsite design technicians need to work together to incorporate the vision and integrity of a building into a structure which can be engineered and manufactured in a factory. This is where the modular/panelised conversation begins.
There are two types of OSM - 3D volumetric modular and 2D panelised. Volumetric refers to entire units or rooms being built to a ‘finish’ in offsite factories and craned into place on site, while panelised refers to individual walls and floors being built at offsite facilities and then erected on site. But why might you specify one over the other?
We make panelised systems at Fusion and they offer developers and contractors a number of benefits:
• They're very flexible in terms of design, meaning bespoke architectural features can be incorporated relatively easily
• Their overall weight is low and they can be easily stacked for transport, meaning you can get multiple rooms or units on a single lorry resulting in very few lorry loads to and from site
• And if design changes do need to be made during a build programme, it’s much cheaper and easier to make them when working with individual panels, giving total cost control to the developer.
Volumetric solutions offer the same benefits as panelised in terms of the OSM process – they’re built in a factory-controlled environment and their manufacture is not impacted by the weather etc. , but the main difference beyond that, is they come as a complete structures. This can mean the internal fit-out, finishes and building services are already installed - leaving the connection of services and their commissioning, external façades and roofing to be completed on site.
But watch this space…at Fusion, we’re developing our panelised system into a ‘Smart Modular’ solution. We start by taking our factory-assembled wall and floor components, together with our patented, pre-insulated external wall system and quickly erect them on site to create a rapidly-weathered shell. The next step is to apply manufacturing principles to complete the building – a true Design for Manufacture and Assembly (DfMA) process. Using BIM, this will mean the precision with which our system is designed, manufactured and assembled on site will integrate seamlessly with other supply chain components – creating a step change in construction processes.
This is an exciting step forward and demonstrates the potential for OSM systems to evolve. Who knows, 10 years from now we could have even more options to talk about, but for 2018 at least the offsite conversation should be broader than just a cursory mention of modular.