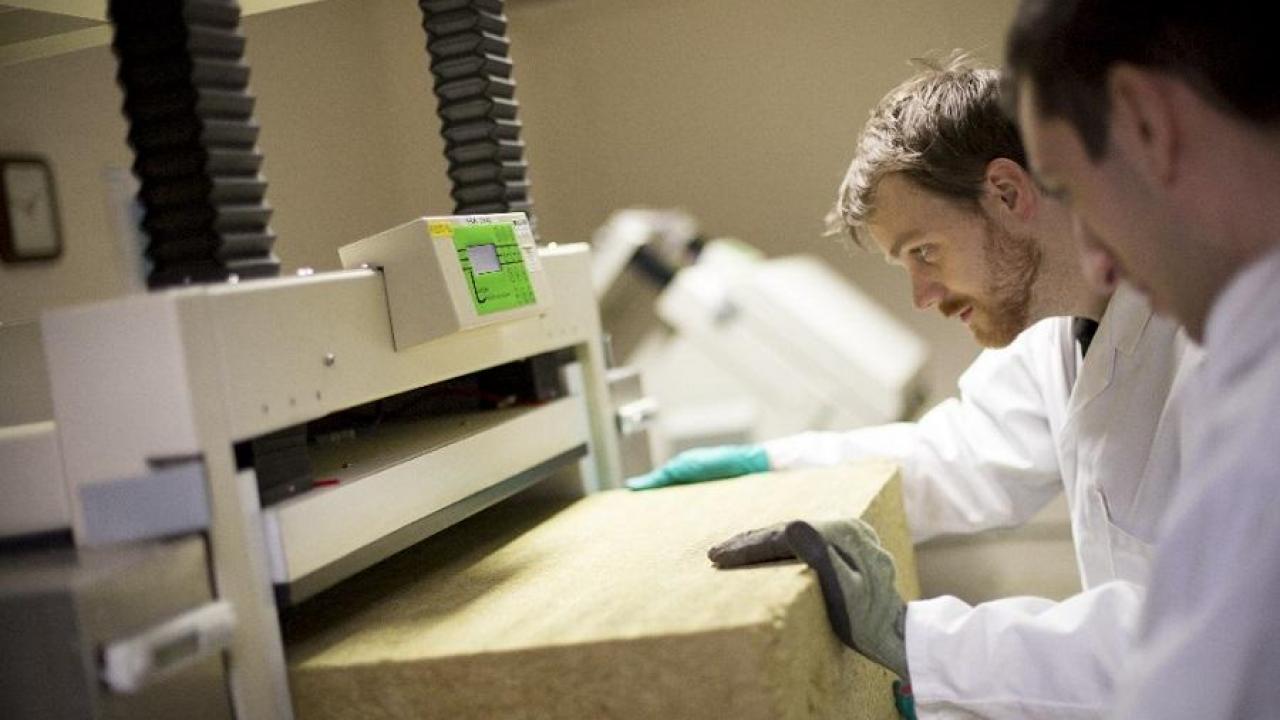
The Product Excellence Programme (PEP) has been introduced to reassure specifiers, designers, architects and contractors that products certified by the British Board of Agrément continue to match their published specification.
For many in the public and private sectors, there exists a lack of trust and understanding of construction products formulations. In addition to this, there is added concern that construction products’ raw materials might have been changed post BBA Certification. Paul Groves investigates how PEP has been designed by the BBA to increase confidence in the industry.
Q: What sets the BBA’s new PEP initiative apart from other post certification schemes in the UK?
A: PEP is a complementary service to the factory production control audits. The fact of checking the characteristics of the different components regularly adds a degree of credibility to the audits and inspections carried out by BBA. In addition, this check is carried out by Test Services, which is a different department, so the analysis is independent of the factory inspection, which adds a greater degree of impartiality and rigor. From the point of view of the consumer, the security and confidence in those products certified by BBA, is maintained and is reaffirmed with the pass of time through these regular PEP checks.
Q: One of the main issues facing the industry post-Grenfell, is a lack of confidence in building products and testing. How does the BBA address this with PEP?
A: While the BBA currently undertakes extensive quality inspections every six months, we found that, after Grenfell, consumers are looking for a higher degree of reassurance and expect products to be tested regularly by a trustworthy and externally assessed independent body.
This need for consistent testing is also noted in the Hackitt Report where focus is given to this aspect of maintenance and care.
With PEP we are able to provide - using a credible, transparent and practical solution - this reassurance not just to architects, building inspectors and specifiers, but also to the whole construction industry and the general public who are questioning the validity of the products being used. In essence, PEP gives extra reassurance that the product they are using continues to match its published specification, and this can only be done with diligent testing over a set period.
Q: What is the difference between PEP and the BBA’s existing auditing and inspection services?
A: PEP is a complimentary service to the factory production control audits. The fact of checking the characteristics of the different components regularly adds a degree of credibility to the audits and inspections carried out by BBA. In addition, this check is carried out by Test Services, which is a different department, so the analysis is independent of the factory inspection, which adds a greater degree of impartiality and rigor. From the point of view of the consumer, the security and confidence in those products certified by BBA, is maintained and is reaffirmed with the pass of time through these regular PEP checks.
Q: How will PEP work in terms of visits to clients, testing and auditing and what are the cost implications?
A: All products enrolled in the Product Excellence Programme will either be tested every year or triennially depending on the product type.
a. Complexity 1 - Are products which possess fire or structural type characteristics
b. Complexity 2 - Products that do not possess fire or structural type characteristics.
In both cases, PEP sampling will be carried out at the same time as the factory production control visit by BBA’s assessors, so there won’t be any extra visit for our clients. PEP tests are priced at a not for profit rate, as we don’t see PEP as a new source of income, hence the prices are at cost levels. Once the samples have arrived to our Product excellence Test Centre in Watford, the client will be informed about the cost and the time-scales and results will be communicated in a short period of time due to the quick turnaround of PEP testing regimes.
Q: What happens if a product fails to pass the new PEP requirements?
A: PEP is a complimentary service to our factory production control audits, results of PEP tests are also submitted to our Product Approval and Certification Team as part of the reviewing process. In the event of a failure, our PAC Team will follow the same procedure as with any other nonconformity found during the auditing process. The issue will be assessed for its significance and corrective action required from the Certificate holder as appropriate. In many cases we would anticipate that the minor problems can be dealt with quickly and will have no consequences for the validity of the Certificate, but where there is doubt concerning whether the product will perform as described in the Certificate, this could result in the immediate suspension and possible subsequent withdrawal of the Certificate in question.
Q: Is this new system still robust enough - who ultimately will police the situation if a product fails testing and does not meet requirements?
A: Withdrawal of certification is not the same as withdrawal of product from market. BBA Certificates are not mandatory, but are widely accepted as authoritative third party evidence of a product’s performance. Wise specifiers will always seek to use products covered by BBA Certification and PEP offers additional reassurance that a product will perform as described within that Certificate.
Q: Is the PEP scheme future-proofed – we could well see further widespread reviews of building regulations on top of the Hackitt Review and will PEP adapt to this?
A: Due to the fact that PEP is a unique program based on product characterisation and a method to track changes that could potentially affect the performance of a BBA certified product: as long as the product continues to match the requirements of the building regulations and the standards to what is been certified, the PEP programme will remain the same and its validity will also remain the same.
Q: Legislation does not always keep pace with technology and new product innovations in the industry, will PEP help to address this dislocation?
A: PEP is a novel initiative in the UK, proactively developed by the BBA to cover certain needs that the public demands and, for which, there were no previous requirements. While it is true that PEP does not imply changes in any technology currently applied in construction, (but instead focuses on ensuring that, over time, construction products do not undergo any change that affects their performance) this information could be easily used to support new technologies in the construction industry. For example, information from PEP could be incorporated directly into the product data sheets that accompany BIM objects.
Regarding the aspect of product innovation, PEP is such a flexible method that, any product, no matter how new, any material, no matter how innovative; It can be characterised and this, related to its performance. therefore, PEP can easily detect possible changes that affect its performance, be it the type of product or material that it is.
Q: What happens with existing clients who have achieved certification with BBA as regards PEP certification?
A: As stated above, PEP is complementary and independent of other services offered by BBA. Therefore, for those customers whose products pass PEP testing, the result will be published on their BBA Certificate page on our website with the year in which the product passed the test. Our clients can also update their product packaging and advertising material with this information.
Q: What if a client simply decides against opting into the PEP scheme?
A: Currently all BBA certified products, have been automatically enrolled in PEP. The basic requirement is to undertake the specified PEP testing regime to ensure that the product remains the same. This can only be done by testing by an independent third party, which has to have a Notified Body Status under the UKAS requirements. There is an option to opt-out from PEP for those clients who have already undertaken these tests within the required timeframe (one year for Complexity 1 products and 3 years for Complexity 2 products). They can submit to our Product Excellence Test Centre a copy of that report and we will check those results against their BBA certificate.
For new products that require certification by BBA, PEP is mandatory, and they will be automatically enrolled without a option to opt out.
Q: What steps are the BBA taking to educate the market about PEP and the benefit of being part of this scheme?
A: There are many initiatives currently happening in the business to educate the market, but the two most significant ones are:
Direct contact with current BBA clients to inform them of PEP so they understand the benefits and the efforts being undertaken by the BBA to improve the confidence and security from the public in the construction products. This communication is ably supported by our working with different industry committees that the BBA sit on.
The second significant thing we are doing to educate the market is, consistent cross platform messaging via press articles on PEP, social media, email communication and recently our CEO Claire Curtis-Thomas recorded a video explaining what BBA PEP is and this is already gaining a lot of watch traction as our clients watch to find out more.
It is important for us that the benefits of PEP and the reasons behind the scheme are quickly understood so that we can continue to push forward in our mission to provide the best possible service to the public, specifiers, architects and designers and give a higher degree of confidence in those products which have systematically proved their full compliance with their certification requirements over a period of time.